Testimonial
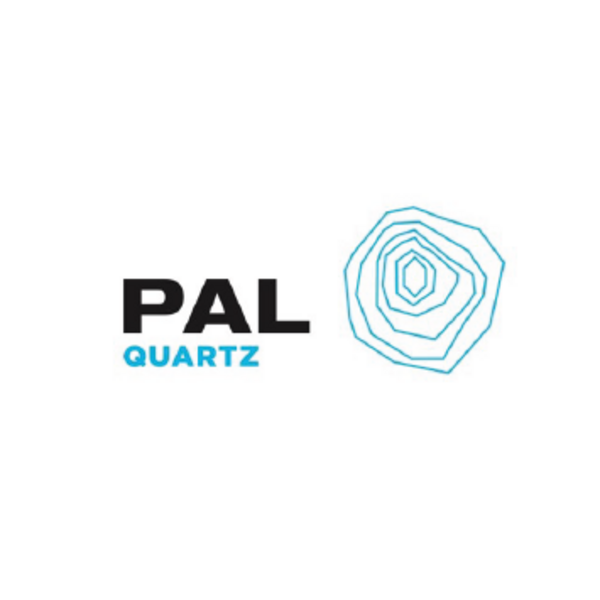
Truly excited
"We are truly excited and impressed by ANZAPLAN professional supports, technical expertise and strategic vision in the process of analyzing the best suited application for this high purity quartz deposit."
Jean Marleau, President and Shareholder, PAL Quartz
Testimonial
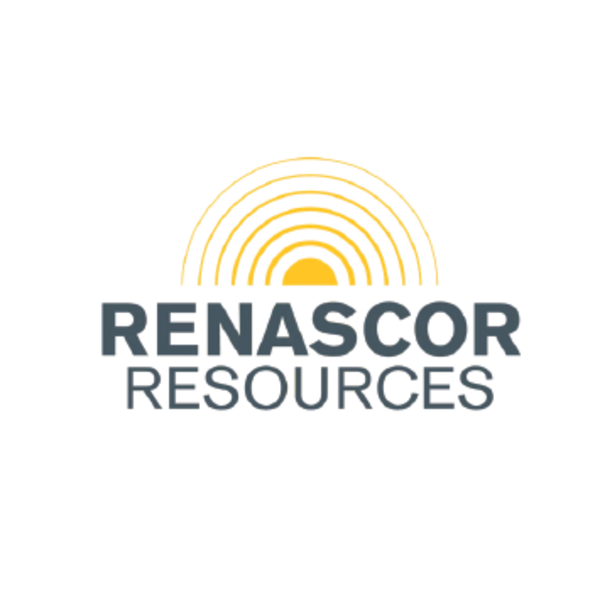
Very pleased
"We are very pleased with the results achieved by leading German independent battery mineral consultancy group ANZAPLAN on our recent optimisation trials for our eco-friendly graphite purification process. The ANZAPLAN team was instrumental in delivering both operational and environmental enhancements."
David Christensen, Managing Director, Renascor Resources
Testimonial
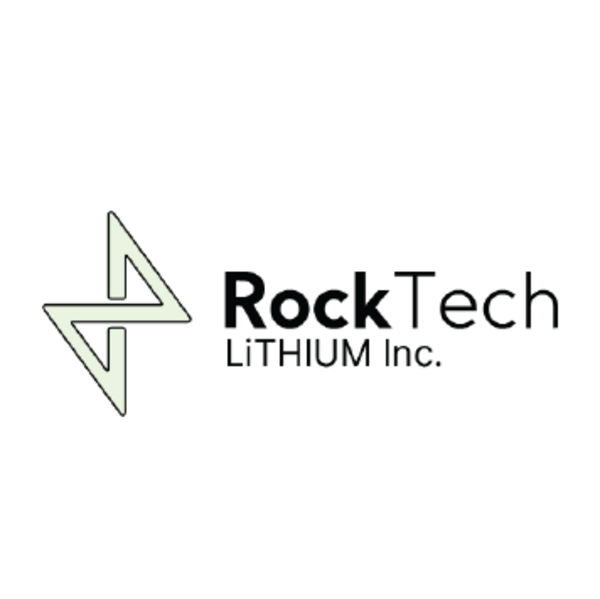
Highly competent team
"We are excited to be working with ANZAPLAN on our Europe-based lithium hydroxide pilot plant. ANZAPLAN’s deep understanding of European industry and highly competent team of processing engineers, chemists and geoscientists will be a great asset to Rock Tech as we continue to advance our European lithium hydroxide converter plant."
Dirk Harbecke, Chairman, Rock Tech
Testimonial
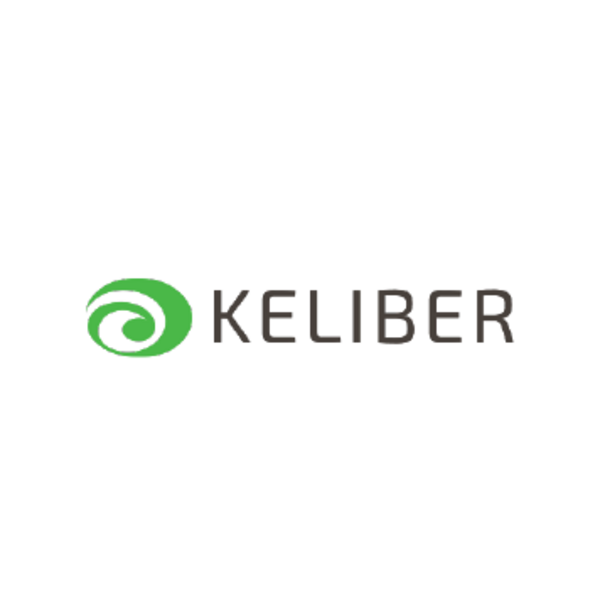
Important milestone
“We are very pleased with the independent confirmation from ANZAPLAN. The verification of battery grade lithium hydroxide from our own ore with the chosen technology is an important milestone for Keliber”
Hannu Hautala, Chief Executive Officer, Keliber
Testimonial
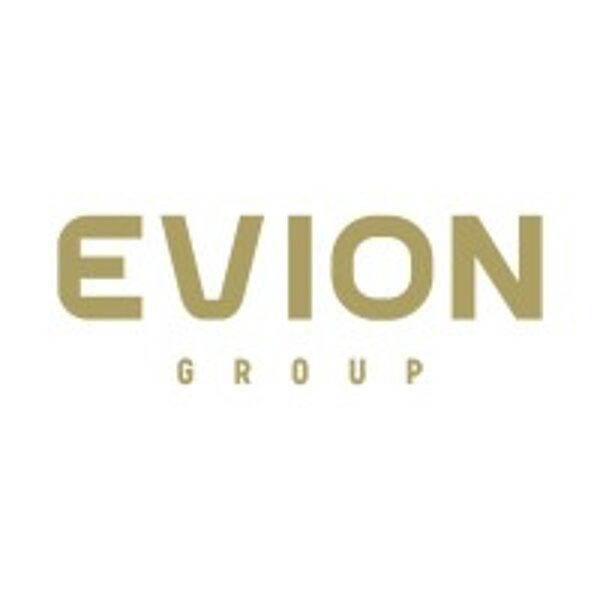
Important component
"ANZAPLAN's test results are an important component towards the end-user qualification process and ultimately off-take agreements, with industry leading manufacturers of lithium ion batteries."
Tom Revy, Managing Director, Evion Group
Testimonial
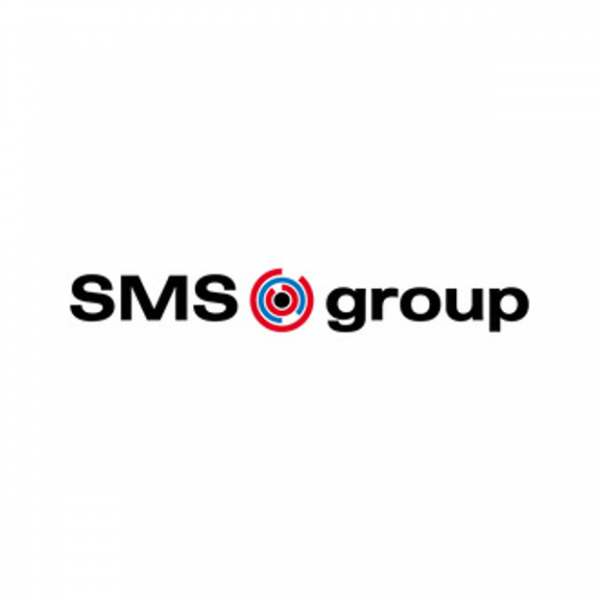
Impressed
"SMS group is impressed with the know-how of ANZAPLAN’s technical team. Their expertise was proven multiple times while working together on projects from different specialty industry segments. Our excellent cooperation has always boosted the projects on their way to success.”
Markus Österreicher, Director of Technology, Research & Development, SMS Group GmbH
Testimonial
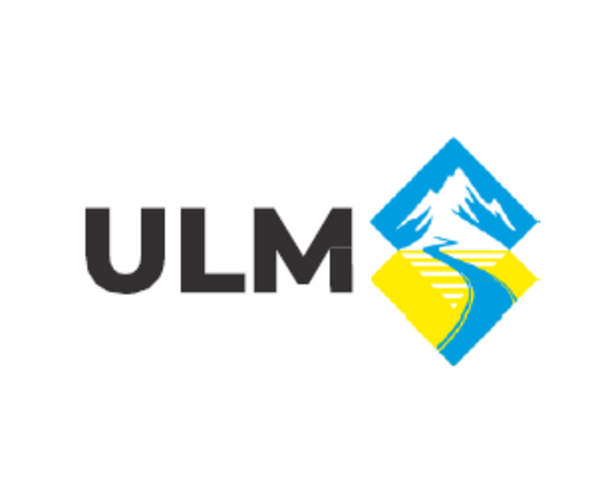
A really enjoyable working experience
"We have been working with ANZAPLAN since 2019 - as part of our lithium exploration effort at Polokhivske deposit in Ukraine. Their huge industry expertise, thorough and systemic approach to doing things, solid business ethics - are the reasons we really enjoy working with ANZAPLAN. Apart from that, the communication has always been superb which allowed us to resolve any commercial or technical issues very quickly."
Igor Zholonkivskyi, Investor Relations Manager, UKR Lithium Mining LLC
Testimonial
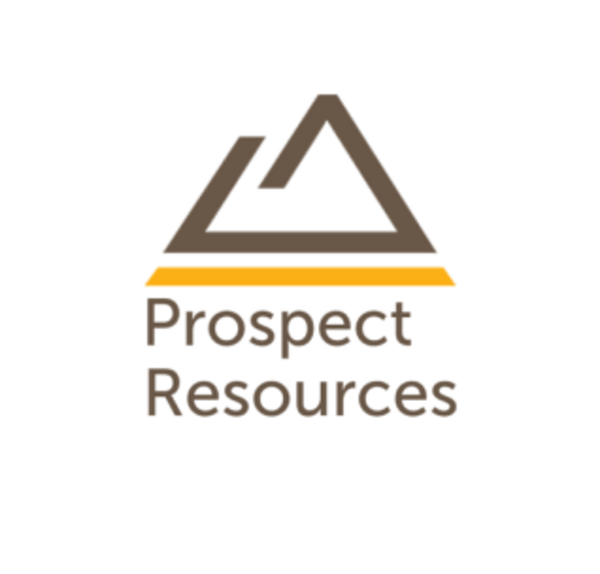
Outstanding
“Prospect resources has immensely benefited from Technical collaboration with ANZAPLAN over the years. To date the support from ANZAPLAN technical teams has been outstanding.”
Sam Hosack, Managing Director, Prospect Resources
Testimonial
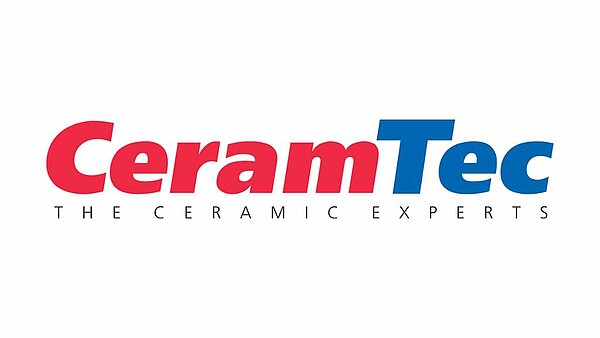
State-of-the-art laboratory
"Upon the occasion of a supplier audit we visited the ANZAPLAN laboratory. We found a state-of-the-art laboratory, very qualified and dedicated employees who work very professionally. Our analytics are in good hands."
Dr. Sabine Walter-Billau, Manager Strategic Procurement Organics & Product Compliance Procurement & Materials Management, CeramTec GmbH
Testimonial
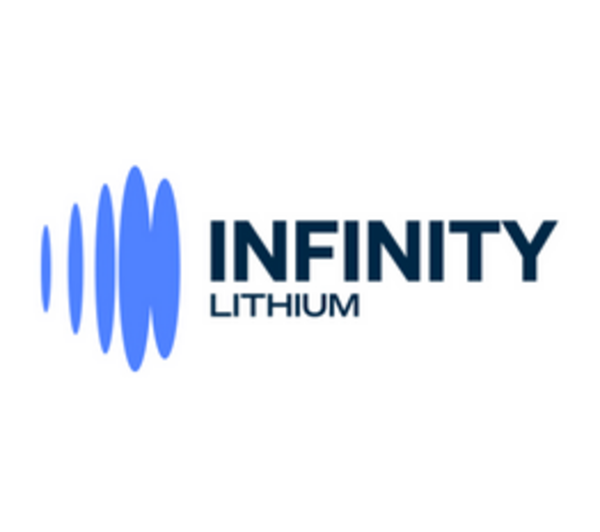
Integral in the development of our sustainable process
“We consider our long-standing partnership with ANZAPLAN integral in the development of our sustainable process that has been tailored for the EU. We are pleased that the team has collaborated with Infinity in confirming the successful production of both battery grade lithium carbonate and hydroxide.”
Ryan Parkin, Managing Director & CEO, Infinity Lithium
Testimonial
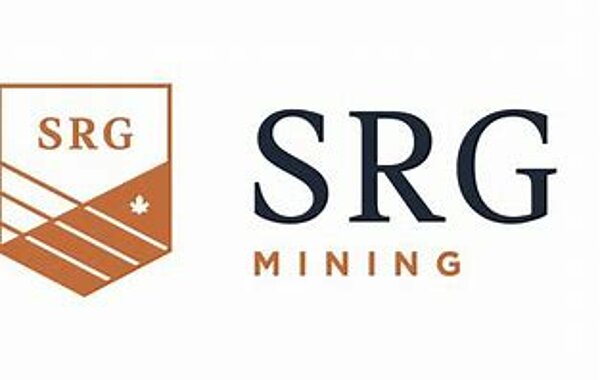
Thinking outside the Box
"As a professional mining executive during my last 30 years in the mining industry I have worked with many consultants and engineering firms and have rare to see a firm such as Anzaplan which offers a high level of competence in their field of expertise. The professionalism, timing and respect of budget in the scope of work are of uttermost importance and the quality of the final output has exceeded my expectations! They really put in all the necessary effort to work In the best interest of the client’s needs and continuously offer solutions and various options while thinking outside of the box. I have learned a lot working with such a wonderful team and look forward to pursuing the next phases of work together!"
Patrick Moryoussef, Chief Operating Officer, SRG Mining
Testimonial
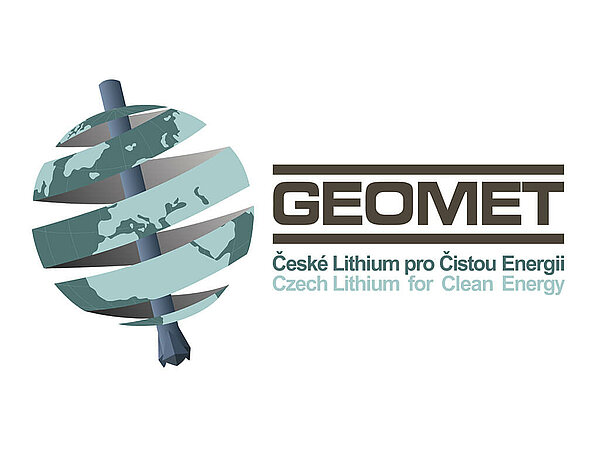
Deep Knowledge
“ANZAPLAN has been of considerable importance to the Cinovec Project as it has developed towards becoming Europe’s largest lithium mine over a period of several years and we thank ANZAPLAN for their continued support. The team’s breadth and depth of knowledge in lithium hydrometallurgy have been highly influential in guiding Geomet towards a viable process flowsheet and we expect to continue to work with ANZAPLAN as new challenges present in the industrial scaling-up of plant and production."
Simon Edwards, Chief Operating Officer, Geomet s.r.o.
Testimonial
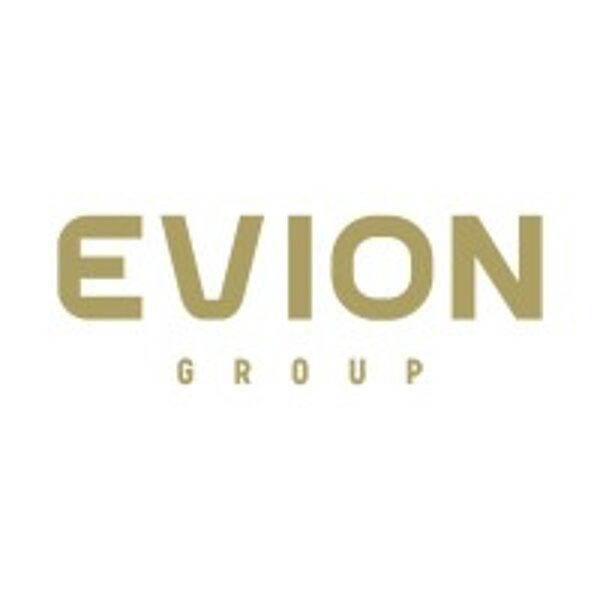
Important component towards end-user qualification
"The test results achieved by ANZAPLAN, further demonstrate the suitability of Maniry Project concentrate, for use in anode production for the lithium ion battery market. The test results are an important component towards the end-user qualification process and ultimately off-take agreements, with industry leading manufacturers of lithium ion batteries."
Tom Revy, Managing Director, Evion Group
Testimonial
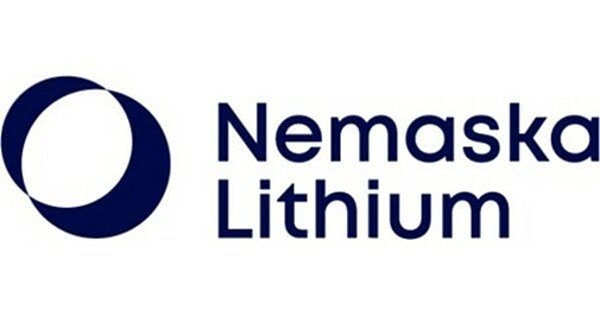
Deep Understanding of the Challenges
"In the last two years, Nemaska did go through a Lithium Hydroxide Plant Design process located in Bécancour in the province of Québec. The Bécancour plant will be fed by Whabouchi’s spodumene deposit. ANZAPLAN provided high level of technical expertise to Nemaska and shows a deep understanding of the challenges faced by the lithium industry. ANZAPLAN´s high value contribution helps Nemaska to target the more significant process and project risks and to identify adequate mitigations. Nemaska is proud of the collaboration with ANZAPLAN leading to a very strong design."
David-Nicolas Allen, Chief process optimization, Nemaska Lithium Inc.
Testimonial
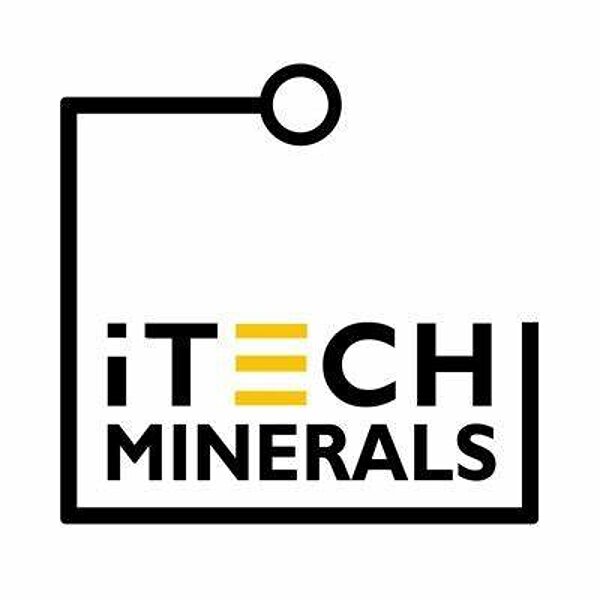
Industry Leader
“iTech is excited to partner with industry leader, ANZAPLAN, to develop a lower cost, eco-friendly process for producing spherical graphite. We believe this will position the Campoona Graphite as a premium product in a market that is quickly transitioning to greener energy storage solutions.”
Mike Schwarz, Managing Director, iTech Minerals
Testimonial
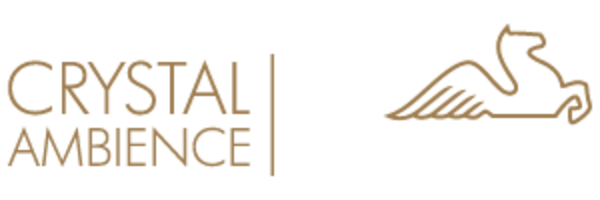
Comprehensive and precise
"All the analyses and procedures we ordered from ANZAPLAN were delivered on time, their report was comprehensive and precise, and the analyses have helped us in solving daily challenges in our glass industry."
Leon Prah, R&D, STEKLARNA ROGAŠKA d.o.o.